1 绪论
1.1 研究背景和意义
在市场经济飞速发展,企业竞争激烈的今天,提高、改进产品的质量和服务水平才是实现企业持续健康发展之道。产品和服务质量的好坏反映了企业素质、发展前景,也是企业经济实力和竞争力的体现。因此,唯有在质量层面精益求精,企业才有可能在行业中赢得一席之地。
1.1.1 研究背景
当前我国经济发展已转向高质量发展阶段,社会对产品质量的需求不断上升。国家将质量强国战略放在突出地位,制定了质量改进的行动指南。质量作为企业经营发展的重要前提,巩固和提升产品的质量有着重要意义。压力容器作为制造业中的重要组成部分,其应用的领域涉及石油化工、机械动力、冶金、核能、航空航天、海洋等行业。它是化工生产的不可或缺的设备,是国家制造水平的衡量。相比于其他制造品,压力容器设计工艺复杂,质量控制环节繁琐,运行过程中一旦出现质量问题,产生的后果比较严重。据国家市场监管局特种设备安监局公布的统计数据(表 1.1),截至 2018 年底,全国共有在役压力容器总量已达到了 394.6 万台,从事特种设备制造企业 17603 家,2018 年内全年共发生压力容器事故 9 起,其中因设备缺陷和安全附件失效引起的事故有 2 起,研究压力容器在制造及运行过程中的质量问题,并进行改进显得尤为迫切。
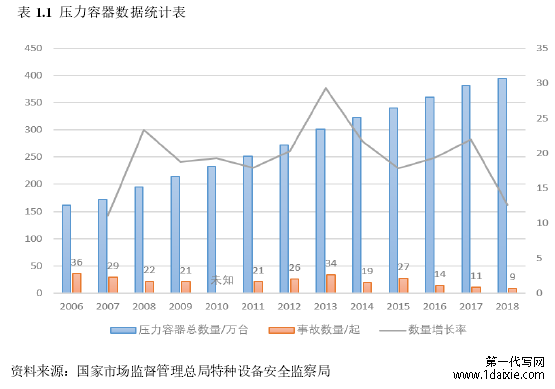
..........................
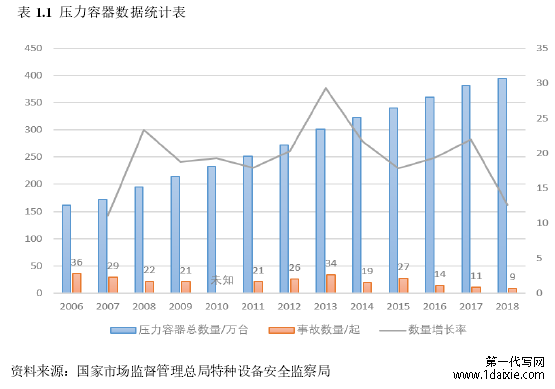
..........................
1.2 国内外研究现状
上世纪 60 年代,全面质量管理(TQM)被提出。在此理论基础之上,国内外学者在质量管理方面开展了如下研究:
1.2.1 国外文献综述
3 A 公司质量管理现状 ................................... 17上世纪 60 年代,全面质量管理(TQM)被提出。在此理论基础之上,国内外学者在质量管理方面开展了如下研究:
1.2.1 国外文献综述
TQM 思想提出以来,国外学者对其在不同行业的应用展开研究。有学者对质量管理和项目管理之间的关系做了一定研究,David James Bryde et al(2007)研究了TQM 和项目管理实践重点之间的关系[1]。Liberatore,M.J. et al(2013)认为质量管理是项目管理的重要组成部分[2]。Fereshteh Farzianpour et al(2015)探讨了 TQM 模式在卫生领域的可行性以及雅兹德医科大学管理者对 TQM 的态度[3]。质量管理是为了优化工序质量、提高产品质量,学者们经常把质量管理和精益生产的思想结合在一起,将二者同步进行。G. V. S. S. Sharma,P. et al(2018)使用 DMAIC 改进过程提高了数控加工过程的工艺水平,改进了 A356 铝合金轮毂制造过程能力指数[4]。Noor,Azlina,Mohd. et al(2012)总结了精益生产和 TQM 的相关理论知识,并且对企业如何利用 TQM 改善公司的精益生产做了相关研究[5]。Laila M.Khodeir et al(2016)指出企业可以通过质量管理对企业的全产业链中存在的浪费、不良波动和僵化等损失现象进行消除来实现企业整体的改善,从而提高企业的竞争力[6]。Afshin Jalali Sohi et al(2016)在借鉴精益思想的基础上针对不同物料提出了不同的精益采购策略,应用将精益-敏捷思想的结合制定合理的采购定点定价机制[7]。Rocio Ruiz-Benitez et al(2017)指出有必要在绿色供应链环境下对传统精益生产方式进行改造,使其在新环境下赋予新的内涵,并根据航天航空部门的实际情况对精益、绿色供应链管理效益进行了研究[8]。还有学者对不同的质量管理的模式进行了比较研究。Everton Drohomeretski et al (2014)识别和分析了精益制造、6σ 以及精益 6σ 三种模型在生产决策领域的差异和互补性,确定在决策领域所遵循的优先次序,并应用于巴西南部的制造企业[9]。Ajay DJewalikar et al(2017)在研究了企业资源计划(ERP)、供应链管理(SCM)、客户关系管理(CRM)等管理思想和技术的基础,结合中小企业的实际情况指出应用 ERP 系统的框架,在分析了三者之间的关系的基础上指出中小企业应该如何实现精益质量管理体系[10]。现在,TQM 已经形成了一门完整的学科,成为许多不同的概念方法和工具的一个包容性的术语。
...........................
2 质量管理相关理论概述
...........................
2 质量管理相关理论概述
2.1 质量管理
关于质量管理的定义有许多,费根堡姆认为:质量管理是“在最经济的水平上、充分满足顾客要求的条件下,进行市场研究、设计、制造和售后服务,把企业各部门研制质量、维持质量和提高质量的活动构成为一体的有效的体系[20]。”朱兰对质量管理的基本定义是:质量就是适用性的管理,市场化的管理[21]。质量管理是指确定质量方针、目标和职责,通过质量策划、控制、保证和改进来实现的全部活动,
关于质量管理的定义有许多,费根堡姆认为:质量管理是“在最经济的水平上、充分满足顾客要求的条件下,进行市场研究、设计、制造和售后服务,把企业各部门研制质量、维持质量和提高质量的活动构成为一体的有效的体系[20]。”朱兰对质量管理的基本定义是:质量就是适用性的管理,市场化的管理[21]。质量管理是指确定质量方针、目标和职责,通过质量策划、控制、保证和改进来实现的全部活动,
这是国际标准化组织(ISO)关于质量管理的定义,该定义角度是质量管理涉及的内容和方法,该定义认为质量管理是具有广泛含义的企业管理活动,其内容包括从质量方针制定到最终用户体验这一过程的全部管理活动[22~24]。
2.1.1 质量管理的发展历程
2.1.1 质量管理的发展历程
质量管理有着较长的发展历史,目前多数学者认为质量管理的发展共经历了三个阶段:质量检验阶段、统计质量控制阶段、TQM 阶段[25]。 (1)质量检验阶段
质量管理活动伴随着生产活动应用而生,最初是依靠操作人员的经验水平来保证产品质量,直到泰勒“科学管理”理论的诞生,产品的质量检验与加工制造相分离开来。随着生产活动的发展,逐渐有了评判产品质量的技术标准的各类检验工具,开始设立专门从事产品质量检验的检验部门,这时是“检验员的质量管理”,这段时期都属于检验质量管理时期,它们的共同特点是通过“事后检验”来评判质量的好坏。
质量管理活动伴随着生产活动应用而生,最初是依靠操作人员的经验水平来保证产品质量,直到泰勒“科学管理”理论的诞生,产品的质量检验与加工制造相分离开来。随着生产活动的发展,逐渐有了评判产品质量的技术标准的各类检验工具,开始设立专门从事产品质量检验的检验部门,这时是“检验员的质量管理”,这段时期都属于检验质量管理时期,它们的共同特点是通过“事后检验”来评判质量的好坏。
(2)统计质量控制阶段
从 19 世纪 20 年代开始,美国数理统计学家休哈特提出的控制和预防缺陷的概念,贝尔研究所提出抽样检验的概念及具体实施方案,开始将数理统计理论应用于质量问题的解决,标志着质量管理进入了一个全新的时代。尽管起初这种方法并未得到普遍的认可,直到第二次世界大战美国国防部决定将数理统计方法应用于质量管理,成立了质量管理方面规划的专门委员会,由专业的质量预防工程师完成质量控制工作,这也标志着质量管理转变为预测质量事故的发生并加以预防的观念。
........................
2.2 质量改进
质量改进是朱兰“质量三元论”的重要内容之一,是通过质量突破来实现前所未有的绩效水平的过程,现代管理学认为质量改进的对象既可以是产品质量也可以是工作质量。质量改进和质量控制具有一定区别,通过质量改进可以消除一些系统问题,而质量控制只能消除一些偶发问题。质量改进和质量控制二者之间又存在一定关系,二者都是为了解决质量问题,只有在质量控制稳定的基础上才能有效的保证质量改进的效果。
2.2.1 质量改进的过程
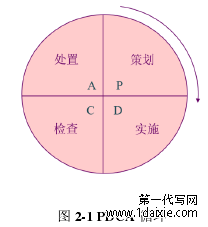
从 19 世纪 20 年代开始,美国数理统计学家休哈特提出的控制和预防缺陷的概念,贝尔研究所提出抽样检验的概念及具体实施方案,开始将数理统计理论应用于质量问题的解决,标志着质量管理进入了一个全新的时代。尽管起初这种方法并未得到普遍的认可,直到第二次世界大战美国国防部决定将数理统计方法应用于质量管理,成立了质量管理方面规划的专门委员会,由专业的质量预防工程师完成质量控制工作,这也标志着质量管理转变为预测质量事故的发生并加以预防的观念。
........................
2.2 质量改进
质量改进是朱兰“质量三元论”的重要内容之一,是通过质量突破来实现前所未有的绩效水平的过程,现代管理学认为质量改进的对象既可以是产品质量也可以是工作质量。质量改进和质量控制具有一定区别,通过质量改进可以消除一些系统问题,而质量控制只能消除一些偶发问题。质量改进和质量控制二者之间又存在一定关系,二者都是为了解决质量问题,只有在质量控制稳定的基础上才能有效的保证质量改进的效果。
2.2.1 质量改进的过程
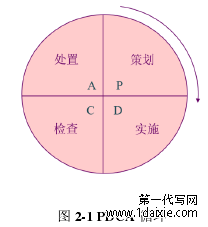
按照PDCA循环的四阶段,进一步将其划分为八个具体的实施步骤:
(1)识别问题:分析企业现状,\识别存在问题,确定改进内容。
(2)分析原因:分析产生问题的全部影响因素。
(3)确定主因:找出产生问题的主要因素。
(4)制定措施:针对主要因素制定改进措施,编写改进计划。
(3)确定主因:找出产生问题的主要因素。
(4)制定措施:针对主要因素制定改进措施,编写改进计划。
(5)执行计划:按既定的措施计划进行实施。
(6)检查效果:对照计划目标,检查验证实际执行情况,评估是否达到了预期的目标效果。
(6)检查效果:对照计划目标,检查验证实际执行情况,评估是否达到了预期的目标效果。
(7)纳入标准:进行改进总结,把实施成功的纳入有关体系文件、管理制度、相关标准中,并巩固和监控已经取得的效果。
(8)未解决问题:对于此循环未解决的问题以及由于质量改进产生的新问题,可以把它们放入下一次 PDCA 过程。
.............................
3.1 公司概况..................................... 17
3.1.1 资源优势 .......................... 17
3.1.2 组织机构设置 ............................. 17
4 A 公司质量改进策划 ........................................... 30
4.1 压力容器质量改进......................................... 30
4.1.1 成立质量改进小组 .................................. 30
4.1.2 改进目标确定 ...................................... 31
5 产品质量改进方案与实施 ......................... 41
5.1 制定对策.............................. 41
5.2 对策实施............................ 43
5 产品质量改进方案与实施
5.1 制定对策
(1)供应商管理
供货商是企业的外部资源,也是供应链系统的重要环节,创建良好供需关系是提高整个供应链效率的关键。由于采购周期短,处理好与供应商的关系就显得尤为重要。
评价选择供应商:选择供应商时,不仅仅对产品的质量、交货期、价格等多种因素进行评价,而且还要重视供应商企业信誉、管理能力、生产规模、财务情况和技术等方面,对供应商进行全面评估,可以有效减少采购风险的发生。
供应商分类管理:通常采用 ABC 的分类管理方式,即根据供应品对企业自身重要性进行具体分类,再把产品对应的供应商划分成若干类别。这种方法可以更好体现出供应商的具体价值,企业可以针对不同种类的供应商,采取相应的供应商管理手段。
完善供应商的绩效评价与反馈机制:为保证供应商管理工作持续有效,对供应商进行管理和监督也是必要的,一方面可以增加企业和供应商之间信息沟通的流畅性,实现信息及时的共享。另外通过建立完善的绩效评价指标体系,根据指标评价的结果对供应商进行及时反馈,可以提高供应商自我改进,更好的完成企业针对产品的采购需求。
..........................
总结
本文在分析 A 公司压力容器制造过程中存在的质量管理问题的基础上,采用传统的三步法来解决问题,找出了问题产生测根本原因,最后针对 A 公司产品的质量问题提出了详细的改进方案和保证措施。
现对本文总结如下:
首先,在了解 A 公司基本概况和质量管理现状的基础上,调查掌握了 A 公司压力容器产品的质量问题,选定焊接一次合格率作为改进内容,进一步分析了影响一次合格率的三个重要因素:原材料、焊接工艺、焊接质量,通过检测数据分析了三个要素存在的问题。
其次,通过对 A 公司无损检测工作质量进行调研,发现无损检测技术应用方面存在错漏检严重、人员技术水平不足和缺乏过程的监督与指导等问题,针对发现的问题,通过因果图等工具对问题全面的分析,找出的产生问题的主要原因,并制定了对应的改进方案,方案实施后检测工作质量有了明显提高。
最后,成立 QC 活动小组通过运用 PDCA 方法来提高焊接一次合格率,经改进后最后提高了焊接的质量,作为本文改进方案和措施的效果说明,验证了将无损检测技术应用到压力容器的质量改进是可行的。
本文虽然针对A公司在无损检测质量管理问题和压力容器产品质量问题上等问题进行研究和分析,提供相应的整改措施和建议,以供A公司产品质量改进参考。然而,本文也难免存在一些不足之处:
(1)由于问题切入点的关系,本文在选取 A 公司质量改进措施时,只从无损检测技术和检测结果发现质量问题这两个角度切入,研究不是很全面。还由于时间问题,同时从两个切入点展开了研究。A公司质量改进效果还需要一段时间进行测量和持续跟踪;
(2)由于积累的数据较少,因此在对问题进行分析的时候,定性分析多而定量分析少,相应措施的数据分析证明材料少,如能增加一定比例的数据分析,将使本文具有更大的说服力;
(3)质量管理是一项系统工程。由于本人知识水平和经验阅历等能力有限,还不能较为全面系统的研究压力容器制造行业和质量管理相关内容。但希望本研究能对其他同类企业的质量管理有所帮助和启发。
参考文献(略)